How to choose the right gypsum powder mill?
Release Time:2024-04-11
Table of Contents
Introduction Of Gypsum
Gypsum is a monoclinic crystal mineral whose chemical composition is calcium carbonate, which has high sound insulation, heat insulation and fire resistance. In addition to being used in construction and industrial raw materials, gypsum can also be used in model making, paint fillers, paper fillers, medical additives, and more.
Usually there are two kinds of gypsum, one is raw gypsum and the other is anhydrite. Gypsum is usually dense or fibrous and is white, red and grey in color. Anhydrite crystals are plate-like and white or off-white in color. The two kinds of gypsum can transform each other under certain geological action.
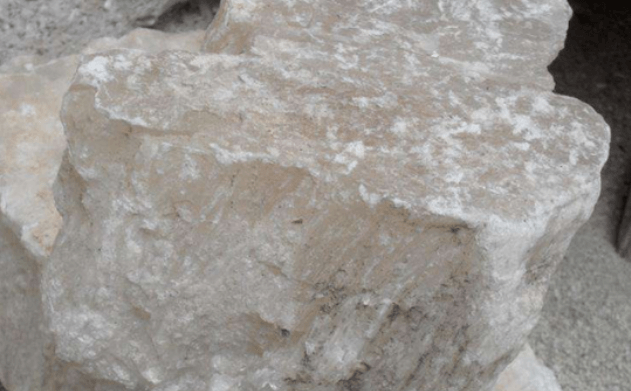

Type Of Gypsum Powder Mill
There are many types of grinding mills available for gypsum grinding, so how to choose a suitable grinding mill?
In general, the commonly used grinding mill for gypsum grinding include Raymond mill, ultra-fine grinding mill, three-ring roller mill, high-strength grinding mill and high-pressure micro-powder mill.
Raymond Mill
Raymond mill is mainly used for grinding non-metallic ores, which can grind gypsum to 325 mesh size. The grinding effect is very good and has high utilization value.
Advantagers of Raymond mill
1. The Raymond mill is a vertical structure, which reduces the floor space of the equipment. From the grinding of gypsum to the formation of the particle size of the finished product, it can be an independent production system without the help of other equipment, and the performance of the complete set is very strong.
2. The screening system of the equipment makes the particle size of the obtained gypsum finished product very uniform, and the sieving rate sometimes reaches 99%, far exceeding other grinding equipment.
3. The important parts are made of good steel, and the wear-resistant parts are also made of good wear-resistant materials, which improves the wear-resistant performance of the equipment and makes the operation more safe and reliable.
4.The electrical system of the equipment adopts centralized control, so that it can basically complete the operation without human operation in the workshop, and the completion effect is very good.
Ultrafine Grinding Mill
The ultra-fine grinding mill is used for ultra-fine powder processing of gypsum. The particle size of the gypsum after processing is finer than other equipment, and the smallest can reach 3000 mesh, which has many performance advantages.
Advantagers of ultrafine grinding mill
1. The parts of the ultra-fine grinding are fixed relatively tightly and have a compact structure, which makes the equipment run more smoothly, and also reduces a part of the floor space.
2. The operation and maintenance are very convenient, the replacement of various parts is very fast, it will not take up too much construction time, and it will not affect the construction progress of the equipment.
3. The output of gypsum is effectively increased, the grinding efficiency is very high, and the overall grinding efficiency of the equipment is improved, thereby improving the economic benefits of customers.
High-strength Grinding Mill
High-strength grinding mill is a new type of grinding equipment, also known as high-strength mill. It is mainly used for high-fine grinding of gypsum. The particle size of the obtained gypsum finished product can be freely adjusted between 80-425 mesh.
a. In the process of processing gypsum with a high-strength grinding mill, it not only runs smoothly but also has very high safety. It will not pose a threat to the safety of operators and can be used with confidence.
b. The structure design is simple and the parts are very compact, making it very convenient to operate and maintain, and the parts can be replaced quickly.
c. The gypsum grinding operation is carried out continuously and the number of failures is very small, which reduces the customer’s operating cost to a certain extent.

Vertical Ultrafine Powder Grinding Mill
The fineness of the gypsum finished product after Vertical Ultrafine Powder Grinding Mill can be adjusted between 500-3000 mesh, and it is mainly used for the ultra-fine powder processing of gypsum.
1. Good quality of finished products: Finished products have high whiteness, fine particle size, narrow particle size distribution, and good particle sphericity. The fineness D97 of the finished powder can reach 3000 meshes, and the content of 2μm can reach up to 60%.
2. High grinding efficiency: save 20~30% power consumption compared with the ball mill.
3. Strong drying capacity: dry and grind raw materials with moisture content as much as 15%.
4. Multifunction: crushing, drying, grinding, separating, and conveying.
5. Low noises and little dust: no direct contact between the grinding rollers and grinding disc, so metallic impact is avoided, and its noises are 20~25 decibels lower. Totally closed negative pressure operation has been employed by this vertical grinding mill, so there is little dust during the operation.
Company Profile
Shanghai Clirik Machine Co., Ltd. has a professional technical force and perfect production capacity. The company’s products are widely used in mining, road construction, bridge construction, housing construction and other industries, crusher, ultra-fine grinding mill, feeder, vibrating screen, sand washing machine, conveyor and other equipment and series of products, all passed the ISO9001:2000 standard quality certification.

Our Technology
Clirik has more than 12,000 square meters of standardized production plant, including a processing workshop, assembly workshop, painting and sandblasting workshop, trial machine debugging workshop, finished product placement workshop, etc. The workshop is equipped with more than 100 high-end CNC machine tools of well-known foreign brands.
From drawing, assembly to debugging, the equipment manufacturing has gone through thousands of processes, including resizing, cutting, grinding, trimming, heating, forging, turning, milling, grinding and drilling, inspection, painting, assembly and test machine. Each manufacturing process is repeatedly verified by our engineers to ensure the reliability and integrity of each device. Raw materials are related to the quality of products. Our engineers have strict requirements on the selection of raw materials. National standard steel is used.

From drawing, assembly to debugging, the equipment manufacturing has gone through thousands of processes, including resizing, cutting, grinding, trimming, heating, forging, turning, milling, grinding and drilling, inspection, painting, assembly and test machine. Each manufacturing process is repeatedly verified by our engineers to ensure the reliability and integrity of each device. Raw materials are related to the quality of products. Our engineers have strict requirements on the selection of raw materials. National standard steel is used.